History and Development of Electromechanical Servo Systems
A modern electromechanical servo system would likely appear as magic to an engineer from 100 years ago. However, the foundation for modern servo systems was laid during that time. In this article, we reflect on the key drivers of servo system development and highlight several milestones in its actual progression.
The development of electromechanical servo systems
The development of electromechanical servo systems involves the convergence of concepts and techniques that have evolved over roughly the past century. This development was fueled by several crucial advancements that humanity underwent and, of course, a significant challenge.
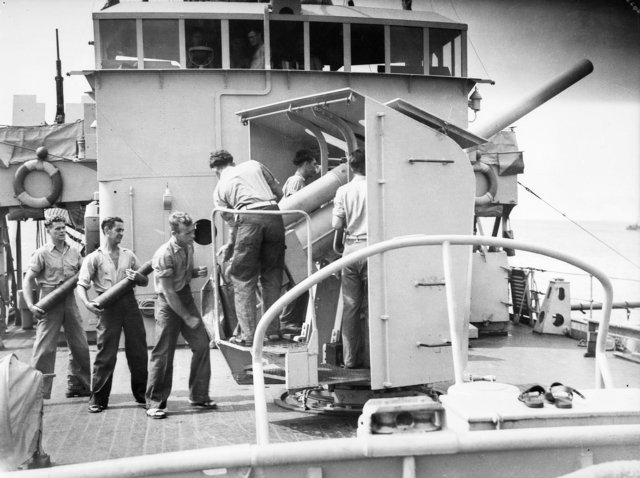
Firstly, the industrial revolution played a significant role. The demand for more efficient production methods for standard and mass-produced goods was a key driver of industrialization, leading to mechanization and subsequently automation of production methods. Servo systems played a pivotal role in a wide range of innovations in this field.
During World War II, servo mechanisms were widely adopted for the first time. Searchlights, radar systems, and cannons on ships and aircraft needed to aim faster and more accurately.
The development of the computer enabled the digitization of servo systems. Digitalization allowed for the design of more powerful controllers, increased the accuracy of the servo system’s tracking behavior, improved stability, and enhanced the system’s resilience to disturbances.
The Servomechanism
Towards the end of the 19th century, Joseph Farcot in France designed a series of closed-loop position systems used to control steamships. In 1873, he published a book titled “Le servo-moteur ou moteur asservi,” describing various control mechanisms he had developed. This marked the birth of the term “servo-moteur” or servomotor and servomechanism.
The fundamental challenge
The fundamental technical challenge that needed to be addressed stemmed from the fact that increasingly larger mechanical devices needed to be positioned more accurately to move or process a product. Manual or “open-loop” control of processes no longer yielded the desired results in terms of response time and accuracy. Over time, a number of basic components were developed to address this issue.
The conversion of electrical energy into mechanical energy was achieved through an electric motor. The development of the electric motor dates back to 1834 when Moritz Hermann Jacobi created the first functional rotating electric motor. Initially, direct current (DC) electric motors were primarily used as the driving element. The development of brushless servomotors began around 1950 and is still used in most servo applications to this day.
To control the motor’s torque and speed, the current through the motor and the supplied voltage needed to be controlled. In the early development of servo systems, this was achieved using an Amplidyne or Metadyne as a current amplifier and an electronic circuit with vacuum tubes. In the 1960s and 1970s, solid-state amplifiers based on MOSFET, transistor, and IGBT elements were introduced.
When controlling position, it is important to measure the actual position of the product. Initially, synchro elements were used for this purpose. A synchro is an electromagnetic angle sensor that, when used as a control transmitter, indicates the difference between the desired position and the actual position. With the rise of microelectronics, encoders started to be increasingly used as position sensors.
Development of Servo Systems: Birth of Electric Motion Control
In 1927, Harold Stephen Black described subtracting a portion of the output of a power amplifier from a portion of the input to reduce signal distortion, particularly for long-distance communication. His invention of the negative feedback amplifier laid the foundation for future signal amplifiers. Negative feedback loops were soon introduced everywhere in both pneumatic and communication equipment.
In the same year that Harold Black published his article on the negative feedback amplifier, Harold Hazen, in his publication “Theory of Servomechanisms,” recognized that negative feedback could be used to improve the behavior of a servomechanism. In the future, the work of both Harolds would be crucial in developing motion control techniques. Electric motion control was born.
Challenges in Closed Loop Systems
The applications for closed-loop systems were on the rise during that time, with most systems designed without a clear understanding of both the dynamics of the process to be controlled and the regulation and actuators involved. Additionally, there were no clear agreements on a uniform language; terms like “feedback” and “stability” were interpreted differently across various disciplines.
Even with the application of negative feedback loops, systems of that time still didn’t perform optimally. The use of pure proportional control was susceptible to overshooting the desired output and required time to smooth out and find stability. Moreover, the system didn’t respond well to sudden disturbances.
PID Control
N. Minorsky [1922] introduced a three-term controller for ship steering, becoming the first to use the proportional-integral-derivative (PID) controller.
The development and implementation of PID control changed everything. PID stands for Proportional, Integral, and Derivative, referring to the different types of gains applied in a controller to correct errors in a closed-loop system. A signal amplified with PID provides a much more robust and smoother response than proportional control alone. The Integral gain eliminated steady-state error, and the Derivative gain reduced response overshoot.
Understanding of Servo and System Dynamics
Early on, awareness of closed-loop system effects existed. On one hand, a system possessed better tracking behavior, but on the other hand, a system was challenging to stabilize due to mechanical play and stiffness (variation in factors like inertia, friction, delays, and noise in electrical circuits). There was a conviction that a servo system needed to be mathematically described to determine system parameters for optimal behavior.
Around the 1940s, differential equations were used to describe system dynamics, and the frequency response technique was used to determine system parameters. Laplace transformations and block diagrams were also employed to describe and analyze servo systems. These depicted the transfer function between the output and input of a servo system.
Stable amplifier design theory was developed by H. Nyquist [1932], who derived the Nyquist stability criterion based on the polar plot of a complex function. In 1938, H. Bode used amplitude and phase frequency response plots of a complex function. He examined closed-loop stability using gain and phase margins. These techniques are the basis for setting and achieving stable systems with desired transient responses.
Digitalization of Servo Systems Enables More Powerful Controllers
Through digitalization, increasingly powerful controllers could be designed for servo systems. Beyond standard PID controllers, it became possible to implement feedforwards, low-pass filters, and bi-quad or notch filters. A 3rd-order profile generator is also used to define the path to be traversed. This results in higher accuracy in the tracking behavior of the servo system, enhancing stability and response to disturbances.
Currently, processors are so powerful, and industrial bus systems are so fast that most machine control application software is implemented in a central machine controller, and the servo controller is driven through a bus system via soft motion.
These PSD servo controllers, combined with SMH servo motors and B-Nimus MC-Pi Prime control, offer unprecedented capabilities compared to the early versions of the technology.
Electromechanical Servo System and Your Application
VARIODRIVE naturally operates at the cutting edge of electromechanical servo systems. We assist machine builders from start to finish, beginning with system architecture based on specifications, then seeking the optimal technical and commercial configuration. We handle system assembly, calculation, simulation, and programming of servo systems. In short, VARIODRIVE is the partner that fully takes the burden of servo system management off the shoulders of machine builders.
Of course, various forms of collaboration are possible. Curious about the possibilities? Contact us at sales@variodrive.nl or call us at +31 186 636 280.