Why is the accuracy and flexibility of servo systems increasing?
What are interesting developments in the field of Motion Control? Managing Director André de Lijser answers this question. In this article, he looks at the evolving market demand, how servo systems have evolved, and the role of (software) integration in increasingly complex motion control applications.
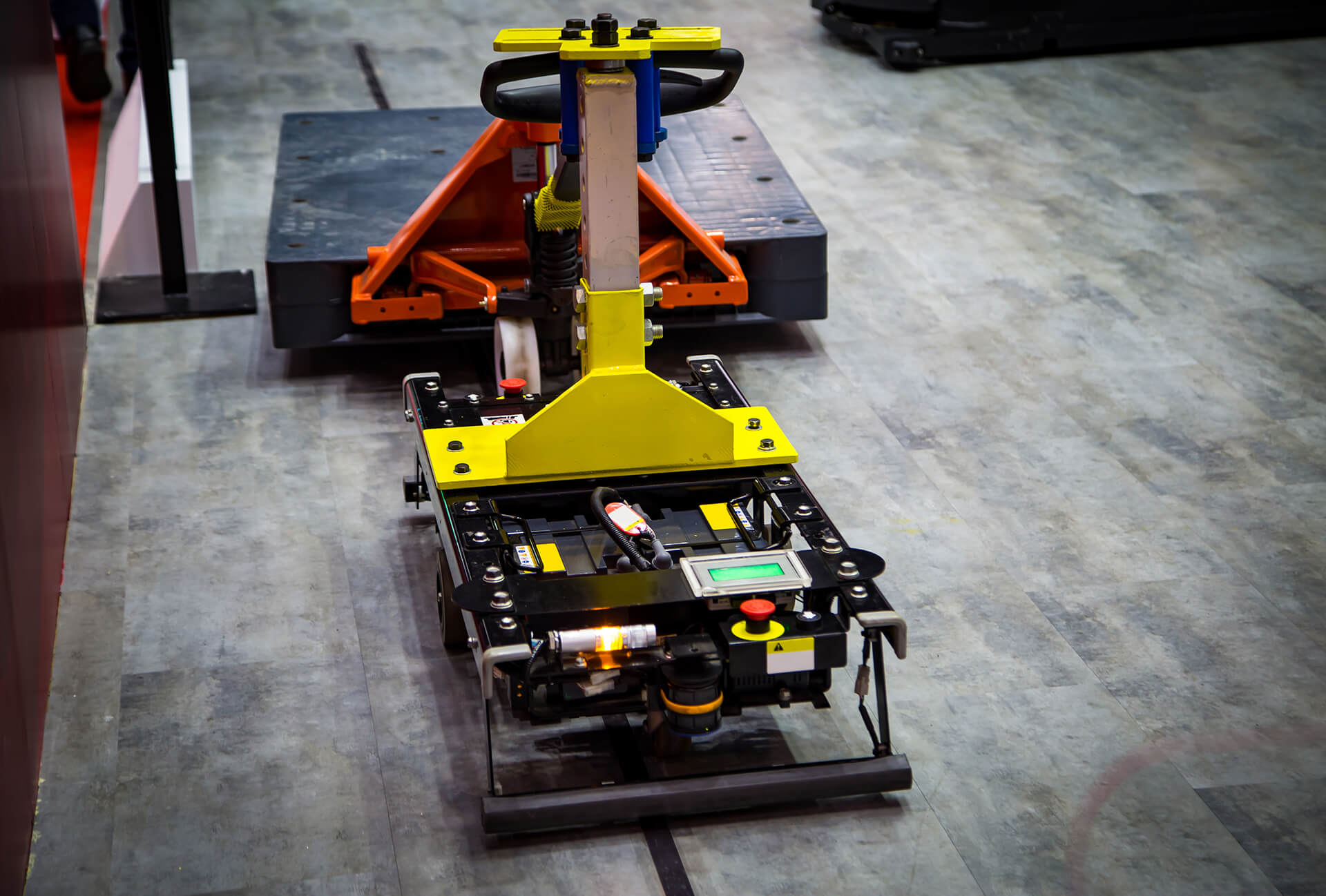
Motion Control is being applied in more and more places, becoming the standard in many markets and product categories. Where pneumatic systems were previously used for simple positioning from A to B, servo axes are now often employed for precise multi-position movements. Markets such as robotics and logistics are undergoing significant advancements thanks to servo technology. Integration and control developments are allowing servo systems to be applied more effectively, leading to efficiency improvements.
This article discusses the following developments and observations:
1. Servo systems enhance machine flexibility.
2. Automation of product handling demands higher accuracy.
3. Motion Control in AGVs becomes more efficient, compact, and targeted.
4. Seamless integration of motion control systems.
5. Native CODESYS: The universal software development environment.
6. Increased accuracy and flexibility of servo systems.
“A machine that used to produce a certain product can, after a few years, be adjusted to produce a slightly different product. While this might be costly or labor-intensive, it’s feasible. However, now machines are being developed that need to handle different products weekly or even daily. This requires a different approach to technology and opens the door to alternative solutions,” explains André Lijser, Managing Director of VARIODRIVE. “Packaging and printing machines are good examples. Intelligent electric axes are being incorporated more, allowing rapid adjustments. These machines need to produce varying products consecutively.”
Automation of product handling demands higher accuracy
VARIODRIVE supplies its Motion Control solutions primarily to Dutch machine builders. As labor becomes costlier and harder to find for their customers, the mechanization of production processes continues. Products and production processes are becoming more complex, demanding higher precision.
“Consider phones as an example. In the past, we had one camera; now, phones have at least three, sometimes more. To improve photo quality—sharper or more appealing—these lenses need to be increasingly precise and accurately positioned. Achieving this requires advanced techniques and machinery.”
When combined with the increased demand for flexibility, it’s clear that advancements in servotechnology are necessary. VARIODRIVE closely follows these developments, curious about the possibilities in 5 or 10 years.
Motion Control in AGVs becomes more efficient, compact, and targeted
Automated Guided Vehicles (AGVs) are finding applications in various environments. VARIODRIVE collaborates with machine builders producing such solutions and notes interesting developments:
“As AGVs are adopted in more settings, the requirements for Motion Control become clearer. A significant trend is the rise of central AGV management systems that communicate externally, ensuring individual vehicles are correctly positioned. This means not every AGV needs these capabilities, allowing for more targeted and efficient solutions.
The Berghof products we offer fit well into this picture. They ensure AGV safety and control, synergizing effectively with upper-level systems. This practical software integration approach is efficient. It’s also a great match with the control systems and motors VARIODRIVE provides.”
Seamless integration of motion control systems
“The simplicity of integrating modern motion control systems has progressed significantly. EtherCAT has become the bus of choice for pure Motion Control. With this system, the central unit can handle all motion profiles, and the servodrive executes them. This places all ‘intelligence’ in one unit—the central control unit—greatly improving manageability. Machine integration is made easier for builders: they no longer need to individually parameterize, program, or configure each unit.”
Native CODESYS: The universal software development environment
“Lastly, there’s software development. In this realm, a crucial system that our Berghof products, for example, natively support is CODESYS. All the functionality of this control software is backed by the Berghof products. CODESYS is a universal development environment for automation products, widely used by many suppliers and software developers. As a result, more engineers and machine builders are becoming proficient in CODESYS. Software engineers are no longer confined to a language supported only by a few brands, but rather they use a language that’s an industry standard for machine builders: Native CODESYS, following the industrial standard IEC61131-3. This simplifies the integration of motion control systems, leading to faster product launches or deliveries with enhanced functionality.”
If you’d like to learn more about the aforementioned developments or engage in discussions about what this means for you as a machine builder, feel free to contact us at 0186-636280.